Unleashing the Power of Rapid Prototype in Metal Fabrication
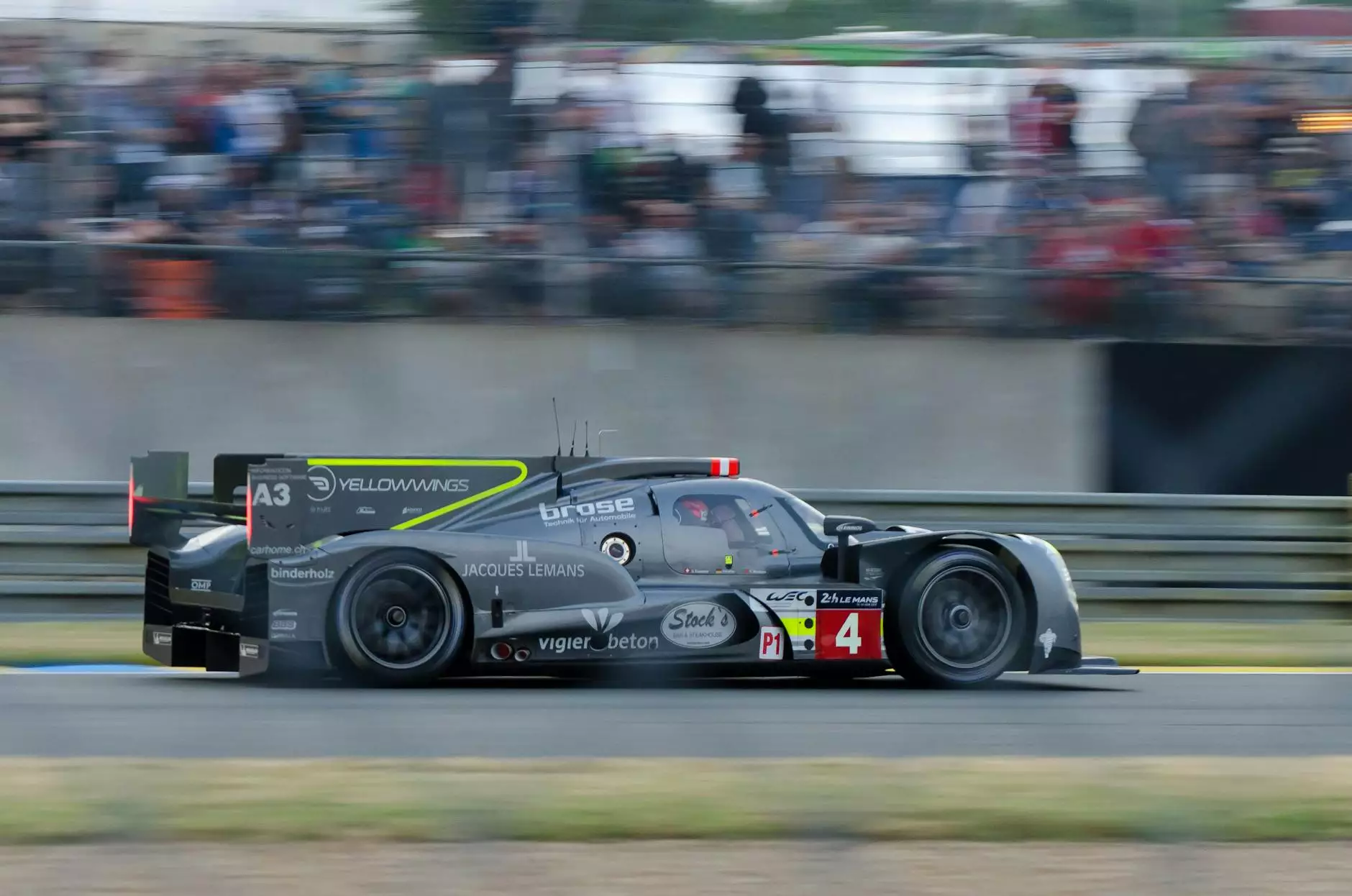
In today's fast-paced industrial landscape, businesses must adapt quickly to meet ever-changing demands. One crucial aspect that is revolutionizing the manufacturing sector is rapid prototype techniques. This article explores how rapid prototyping is transforming metal fabrication, enhancing product design, and driving innovation, with a particular focus on the exemplary services offered by Deep Mould.
Understanding Rapid Prototyping
Rapid prototyping refers to the process of quickly constructing a scale model of a physical part or assembly using 3D computer-aided design (CAD) data. This innovative method allows manufacturers to create prototypes faster and at a lower cost compared to traditional techniques. By embracing rapid prototyping, businesses can significantly reduce the time-to-market for new products, improve design accuracy, and foster creativity.
Benefits of Rapid Prototyping in Metal Fabrication
The integration of rapid prototyping in metal fabrication offers numerous benefits that can reshape the manufacturing landscape:
- Speed and Efficiency: Rapid prototyping enables manufacturers to create prototypes swiftly, facilitating faster feedback loops and reducing the overall development time.
- Cost-Effectiveness: By utilizing prototypes, businesses can identify design flaws early, avoiding costly revisions during mass production.
- Enhanced Design Flexibility: Designers are free to experiment with different shapes, sizes, and materials, leading to more innovative products.
- Improved Communication: Physical prototypes serve as tangible representations of ideas, bridging the gap between designers, engineers, and stakeholders.
- Testing and Validation: Prototypes allow for thorough testing, ensuring that the final product meets performance expectations and industry standards.
How Rapid Prototyping Works
The process of rapid prototyping typically involves several key steps:
1. Conceptualization and Design
The first step involves translating ideas into a CAD model. This digital representation serves as the blueprint for the prototype, ensuring accuracy and detail.
2. Material Selection
Choosing the right materials is crucial in the prototyping phase. Depending on the project's requirements, various metals and alloys can be selected to ensure that the prototype aligns with the final product.
3. Prototyping Technique Selection
Several techniques exist in rapid prototyping, including:
- Stereolithography (SLA): A method that uses a UV laser to solidify photopolymer resin layer by layer.
- Fused Deposition Modeling (FDM): A technique that extrudes thermoplastic material to build prototypes linearly.
- Selective Laser Sintering (SLS): Uses a high-powered laser to fuse powdered metal, creating robust prototypes.
4. Prototype Production
Once the prototyping technique is selected, the production process begins. This stage often allows for adjustments and iterations based on initial feedback.
5. Testing and Finalization
After constructing the prototype, thorough testing is conducted. Feedback from testing can lead to necessary modifications, ensuring that the final product is optimized for performance.
Applications of Rapid Prototyping in Metal Fabrication
Rapid prototyping has a wide array of applications across various industries. Here are some noteworthy examples:
- Aerospace: Prototyping allows for the creation of lightweight, high-performance components essential for aerospace engineering.
- Automotive: The automotive industry leverages rapid prototyping to design complex parts that enhance vehicle performance.
- Medical Devices: Prototypes for surgical instruments and implants ensure that they meet rigorous health standards before mass production.
- Consumer Electronics: Rapid prototyping aids in designing electronic casings and internal structures that are both ergonomic and functional.
Deep Mould: Pioneering Rapid Prototyping Solutions
At Deep Mould, we pride ourselves on being at the forefront of the metal fabrication industry. Our state-of-the-art rapid prototyping services enable businesses to bring their concepts to life with unparalleled precision and speed. Here's what sets Deep Mould apart:
Advanced Technology
We utilize the latest in 3D printing and manufacturing technology, allowing us to produce prototypes that are not only accurate but also high in quality. Our equipment is regularly updated to incorporate advancements in the field, ensuring that our clients receive the best possible products.
Expert Team
Our skilled engineers and designers bring extensive experience and expertise to every project. We collaborate closely with clients to understand their needs and translate their vision into reality.
Commitment to Quality
Quality is at the heart of our operations. Every prototype undergoes rigorous testing to ensure it meets both the intended design specifications and industry standards.
Conclusion
Incorporating rapid prototype into metal fabrication processes is no longer just an advantage; it is a necessity for businesses looking to thrive in today’s competitive environment. The ability to rapidly develop and iterate on designs not only accelerates product innovation but also enhances overall operational efficiency.
With Deep Mould’s cutting-edge rapid prototyping solutions, manufacturers can transform their ideas into tangible products that meet market demands. As we move forward into an increasingly dynamic industrial landscape, the investment in rapid prototyping will undoubtedly yield significant returns for those who embrace it.
Take the Next Step
If you are ready to revolutionize your metal fabrication processes through the power of rapid prototyping, contact us at Deep Mould. Let's innovate together and set your business on the path to success!