Engine Oil Coolers: The Key to Maintaining Optimal Diesel Engine Performance
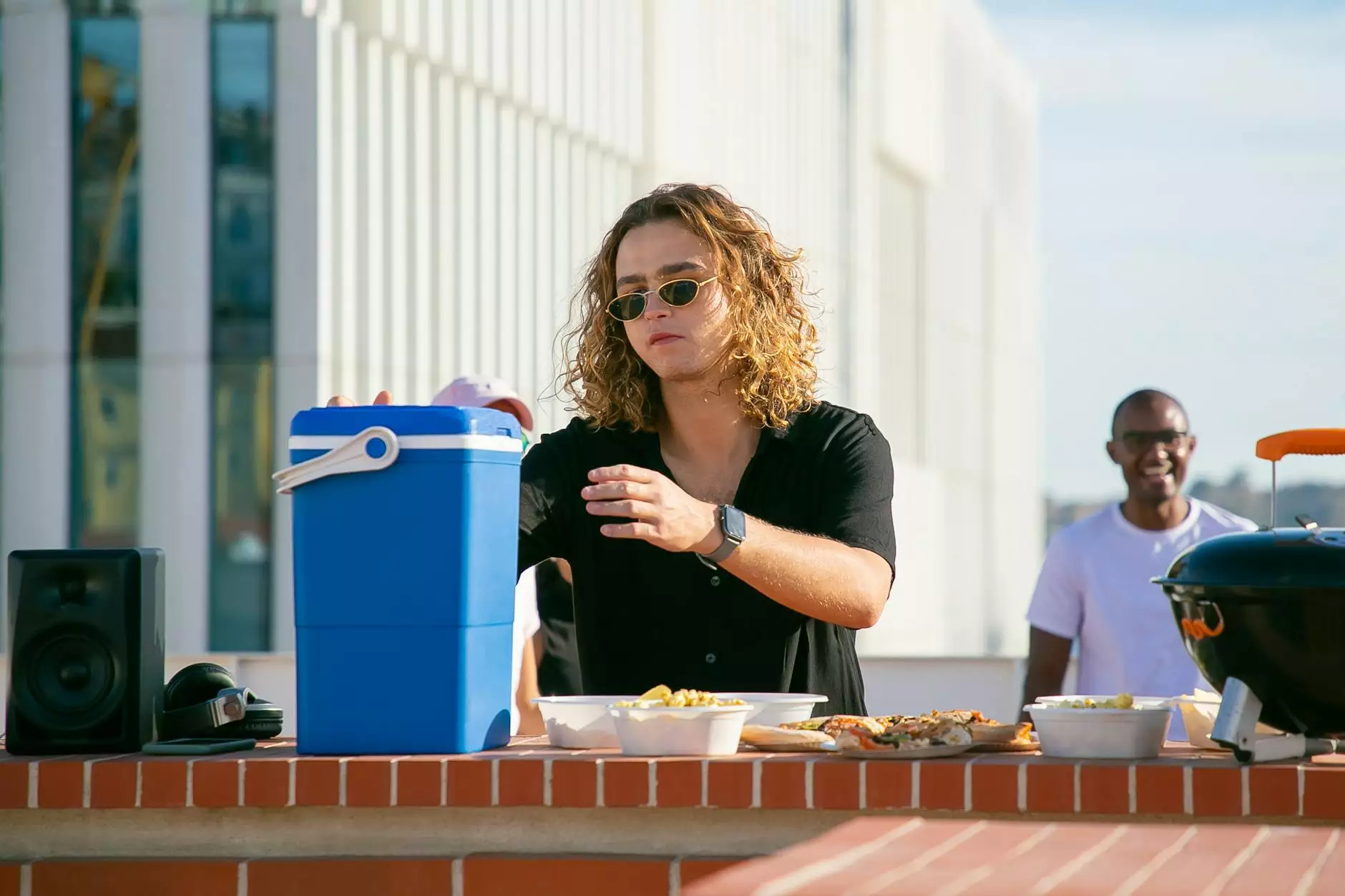
In the highly competitive realm of diesel engine operations, maintaining the peak performance and extending the lifespan of your machinery is paramount. Among the numerous components that contribute to the seamless functioning of diesel engines, engine oil coolers stand out as critical yet often overlooked parts. Their role in regulating oil temperature is vital, ensuring that engines operate efficiently, reliably, and with minimal wear and tear.
Understanding the Importance of Engine Oil Coolers in Diesel Engines
Engine oil coolers are specialized heat exchange devices designed to lower the temperature of engine oil as it circulates through the diesel engine. Diesel engines generate substantial heat due to their high compression ratio and combustion process. Excessive heat can cause oil breakdown, reduce lubrication efficiency, and ultimately lead to engine damage. By effectively cooling the engine oil, these components protect vital engine parts from thermal stress and mechanical wear.
How Do Engine Oil Coolers Work?
The operation of an engine oil cooler involves a simple yet efficient process, primarily relying on heat transfer principles. The cooler typically comprises a series of fins and tubes that facilitate the transfer of heat from the hot oil to a cooling medium, usually air or coolant fluid.
- Step 1: Hot oil from the engine flows into the oil cooler through a series of passages.
- Step 2: As the oil passes through the cooler, heat is transferred from the oil to the cooler’s metal surfaces.
- Step 3: The heat is then dissipated to the surrounding air or coolant fluid, effectively lowering the oil temperature.
- Step 4: The cooled oil returns to the engine, ready to lubricate and protect engine components.
This continuous process ensures that the engine oil maintains an optimal temperature range, typically between 180°F to 220°F (82°C to 104°C), depending on the engine specifications.
The Critical Role of Engine Oil Coolers in Diesel Engine Efficiency
Maintaining the ideal operating temperature is essential for several reasons:
- Preventing Oil Degradation: Excessive heat causes engine oil to oxidize and break down quicker, reducing its lubrication properties. Engine oil coolers help preserve oil quality, ensuring consistent lubrication.
- Reducing Wear and Tear: Optimal oil temperature minimizes friction between moving parts, decreasing wear, and prolonging engine life.
- Enhancing Fuel Efficiency: A well-regulated engine temperature reduces mechanical resistance, leading to better fuel economy.
- Mitigating Overheating Risks: Overheated engines can suffer severe damage, including warped pistons, cracked cylinders, and blown head gaskets. Oil coolers act as a first line of defense against such issues.
- Supporting Turbocharged and High-Performance Diesel Engines: These engines generate more heat; hence, efficient cooling systems are vital for sustainable operation.
Choosing the Right Engine Oil Cooler for Your Diesel Engine
Selecting an appropriate engine oil cooler is fundamental to ensuring effective temperature regulation. Several factors influence this choice:
- Engine Size and Power Output: Larger, more powerful engines generate more heat, necessitating larger or more efficient coolers.
- Type of Diesel Engine: Different engine designs—whether stationary, mobile, or industrial—have specific cooling requirements.
- Compatibility: Ensure the cooler model fits your engine's specifications, including mounting points and flow capacity.
- Corrosion Resistance: Opt for coolers made from materials resistant to corrosion, especially in harsh environments.
- Material Quality: Aluminum and brass are common materials with excellent heat transfer properties and durability.
Integration and Maintenance of Engine Oil Coolers
Proper Installation
Correct integration of the engine oil cooler into the diesel engine's cooling system is crucial. It should be installed in a location with adequate airflow or coolant access, and secured firmly to prevent vibrations and damage. Proper fittings and sealing are essential to prevent leaks.
Routine Inspection and Maintenance
To maximize the lifespan and efficiency of your oil cooler, routine maintenance is essential:
- Regularly check for leaks or corrosion.
- Clean fins and passages to prevent clogging from dirt, debris, or sludge.
- Ensure coolant levels are adequate if used in conjunction with a coolant-based cooler.
- Replace worn or damaged components promptly to prevent cooling failure.
The Future of Engine Oil Coolers in Diesel Technology
As diesel engines evolve, so does the technology of cooling systems. The future points toward the integration of smart cooling systems equipped with sensors and IoT connectivity that monitor oil temperature in real-time and adjust cooling capacity dynamically. Advances in ultra-efficient heat exchangers, lightweight materials, and environmentally friendly coolants are also shaping the industry.
Advantages of Sourcing High-Quality Engine Oil Coolers from client-diesel.com
Partnering with client-diesel.com ensures access to premium spare parts, including a wide range of engine oil coolers tailored for various diesel engine types and brands. The advantages include:
- Superior Quality Materials: Ensuring durability against extreme operating conditions
- Precision Engineering: Perfect fit and optimal heat transfer efficiency
- Comprehensive Compatibility: Compatible with leading diesel engine models and brands
- Reliable Supply Chain: Fast turnaround and consistent availability of parts
- Expert Support and Consultation: Assistance in selecting the right cooler for your engine
Enhancing Your Diesel Engine’s Longevity with Proper Cooling Systems
The longevity of diesel engines heavily depends on effective thermal management. Incorporating high-quality engine oil coolers is a proactive measure that offers multiple benefits:
- Reduced Downtime: Fewer repairs due to thermal stress-related failures.
- Extended Maintenance Intervals: Less frequent oil changes and servicing.
- Cost Savings: Fewer engine repairs and longer-lasting equipment.
- Environmental Benefits: Improved fuel efficiency and reduced emissions.
Conclusion: Why Every Diesel Operator Should Prioritize Engine Oil Cooling
In the realm of diesel engine operations, impeccable cooling solutions are central to maximizing operational efficiency, reducing operating costs, and safeguarding investments. The engine oil cooler is a vital component that ensures engines run within optimal temperature ranges, preventing overheating, oil breakdown, and mechanical failures.
By choosing top-quality engine oil coolers from trusted spare parts suppliers like client-diesel.com, diesel engine operators can achieve remarkable performance, durability, and reliability. Emphasizing proper installation, maintenance, and continuous upgrades aligned with technological advances will reinforce your engine’s resilience and efficiency for years to come.
Investing in superior cooling systems is not just a maintenance decision—it's a strategic move toward sustainable and profitable diesel operations.