Electric Injection Molding: A Revolution in Manufacturing
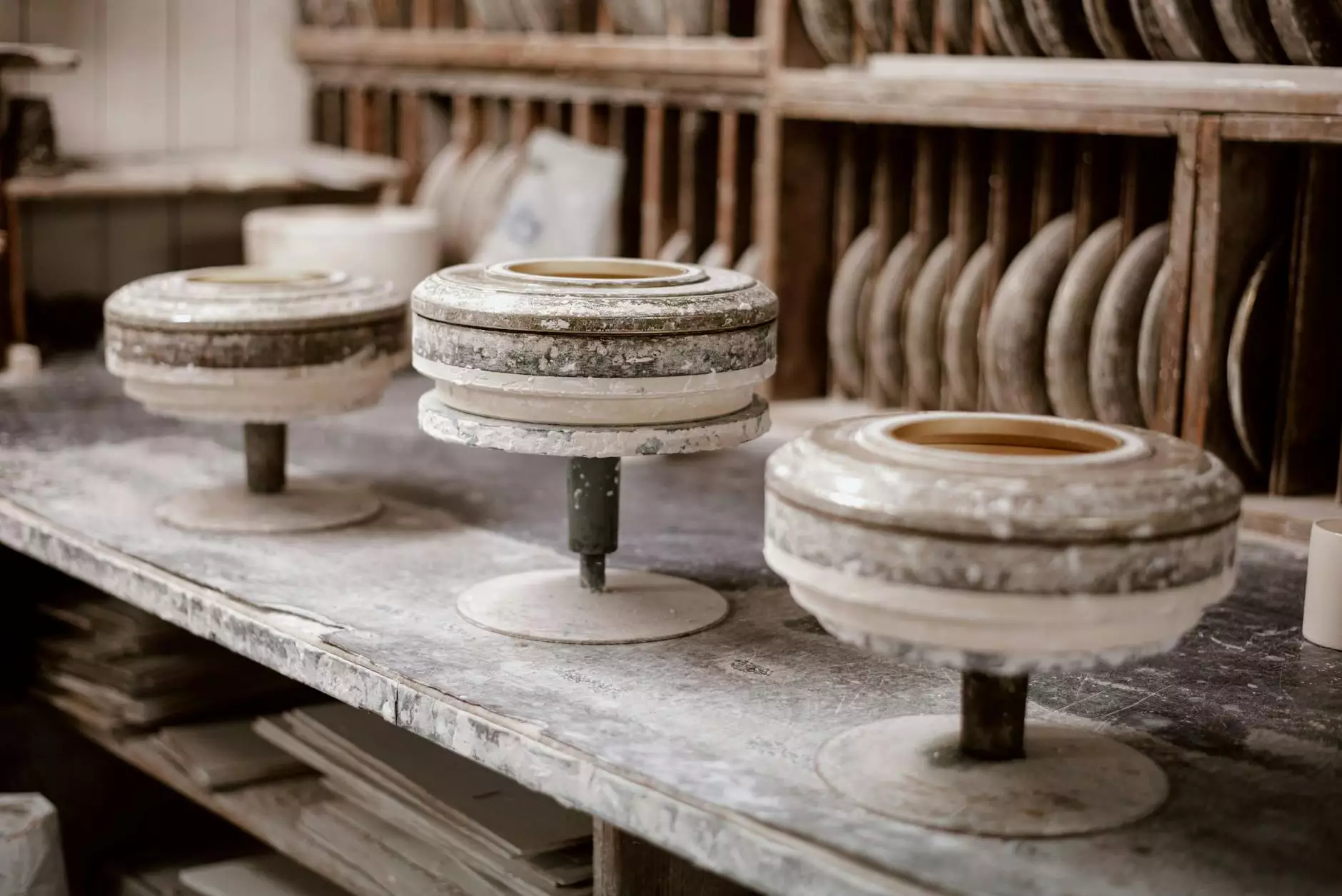
In the ever-evolving landscape of manufacturing technologies, electric injection molding stands out as a game changer that is reshaping how products are made. This cutting-edge technology is characterized by its precision, efficiency, and ability to produce high-quality components in a sustainable manner. In this comprehensive article, we will explore the myriad benefits of electric injection molding, how it compares to traditional hydraulic systems, and its implications for the future of manufacturing. Let's delve deeply into this innovative process that is paving the way for a smarter industrial era.
Understanding Electric Injection Molding
At its core, electric injection molding involves the use of electric motors to power the injection process, rather than relying on hydraulic systems. This modernization brings about numerous benefits that not only improve operational efficiency but also enhance the overall product quality. Here’s a closer look at the basic principles behind electric injection molding:
- Precision Control: Electric injection molding machines offer superior control over the injection process. This allows manufacturers to achieve greater consistency in part dimensions and weight, reducing defects and waste.
- Energy Efficiency: By using electric motors, these machines consume less energy compared to their hydraulic counterparts. This is not only cost-effective but also environmentally friendly.
- Reduced Cycle Times: The speed of electric motors allows for faster cycle times. This means that manufacturers can produce more units in less time, thereby increasing throughput.
Benefits of Electric Injection Molding Compared to Traditional Methods
The transition from hydraulic to electric injection molding is not just a trend—it’s a necessity in an era where efficiency and sustainability are paramount. Below, we highlight major advantages of electric injection molding over traditional methods:
1. Enhanced Energy Efficiency
With rising energy costs and a growing emphasis on sustainability, energy efficiency is a crucial factor for manufacturers. Electric injection molding machines leverage electric motors that only use energy when necessary, unlike hydraulic machines that run continuously. This results in:
- Up to 70% energy savings: Electric systems can significantly reduce energy consumption, leading to lower operating costs.
- Lower carbon footprints: By minimizing energy usage, manufacturers can reduce their environmental impact, aligning with global sustainability goals.
2. Superior Precision and Quality
Accuracy is vital in manufacturing, particularly in sectors like automotive, aerospace, and medical equipment. Electric injection molding offers:
- Exact control: The ability to finely adjust parameters such as injection speed and pressure leads to exceptionally high-quality products.
- Consistency in production: Reduced process variability results in fewer defects and rejections, promoting higher product quality without extensive rework.
3. Reduced Maintenance Costs
Electric injection molding machines are generally designed with fewer moving parts compared to hydraulic machines. This simplicity results in:
- Lower maintenance frequency: Fewer components that can wear and tear mean less downtime for maintenance.
- Longer lifespan: The inherent reliability of electric systems often translates to a longer operational life.
4. Environmentally Friendly Operation
In today's eco-conscious market, using technology that is less harmful to the planet is a key competitive advantage. Electric injection molding is inherently more environmentally friendly for several reasons:
- Reduced hydraulic oil usage: Eliminating hydraulic fluid means reduced risk of leaks and less contamination of waste streams.
- Lower noise levels: Electric machines operate much quieter than hydraulic systems, contributing to a healthier work environment.
Applications of Electric Injection Molding
Electric injection molding technology is versatile and finds application across various industries. Some of the most notable applications include:
1. Automotive Industry
In the automotive sector, the demand for lightweight and precision-engineered components is ever-increasing. Electric injection molding allows manufacturers to produce:
- High-performance parts: Engine components, control panels, and interior fittings can all benefit from the precision offered by electric molding.
- Complex geometries: The technology can easily handle intricate designs, allowing for more innovative automotive solutions.
2. Consumer Goods
From household appliances to electronic devices, the consumer goods sector demands high-quality, cost-effective production methods. Electric injection molding supports this by:
- Streamlining production processes: Faster cycle times and improved accuracy lead to higher throughput, reducing time to market.
- Enhancing product aesthetics: The precision capability allows for better surface finishes and intricate designs.
3. Medical Devices
The production of medical devices requires strict adherence to quality standards. Electric injection molding ensures:
- Compliance with regulations: The high precision and quality control help manufacturers meet stringent health regulations.
- Customization: Electric systems easily adapt to produce tailored components for various medical applications.
Future of Electric Injection Molding
The future of electric injection molding seems bright as the technology continues to advance. Key trends to watch include:
1. Integration with Industry 4.0
The move towards smart manufacturing means electric injection molding machines will likely integrate more with IoT and automation technologies. This will lead to:
- Real-time monitoring: Enhanced data collection and analytics to optimize production processes.
- Predictive maintenance: Using AI to predict machine failures before they occur, thus reducing downtime.
2. Customization and Flexibility
As consumer demands evolve, the need for customization in manufacturing increases. Electric injection molding is poised to adapt by:
- Supporting smaller production runs: The flexibility of electric systems allows manufacturers to produce low quantities without significant losses.
- Rapid prototyping capabilities: Faster adjustments in design can lead to quicker development times for new products.
3. Increased Focus on Sustainability
With sustainability being a driving force in manufacturing, electric injection molding aligns perfectly with this ethos. Future developments may include:
- Alternative materials: The adoption of biodegradable or recycled materials through electric molding processes.
- Energy-saving innovations: Continuous improvements in motor technologies to further enhance energy efficiency.
Conclusion
In summary, electric injection molding represents a significant leap forward in manufacturing technology, offering unparalleled benefits in terms of efficiency, precision, and sustainability. Industries ranging from automotive to consumer goods and medical devices are already witnessing the transformative effects of this technology.
As businesses continue to invest in electric injection molding, the landscape of manufacturing will undoubtedly keep evolving, driven by innovation and the need for sustainable practices. Companies that embrace this change will position themselves advantageously in an increasingly competitive market. The future is electric, and electric injection molding is at the forefront of this exciting transformation.
For further inquiries into electric injection molding systems and their applications in your business, visit deepmould.net.