Exploring the Role of Silicone Prototype Manufacturers in Modern Business
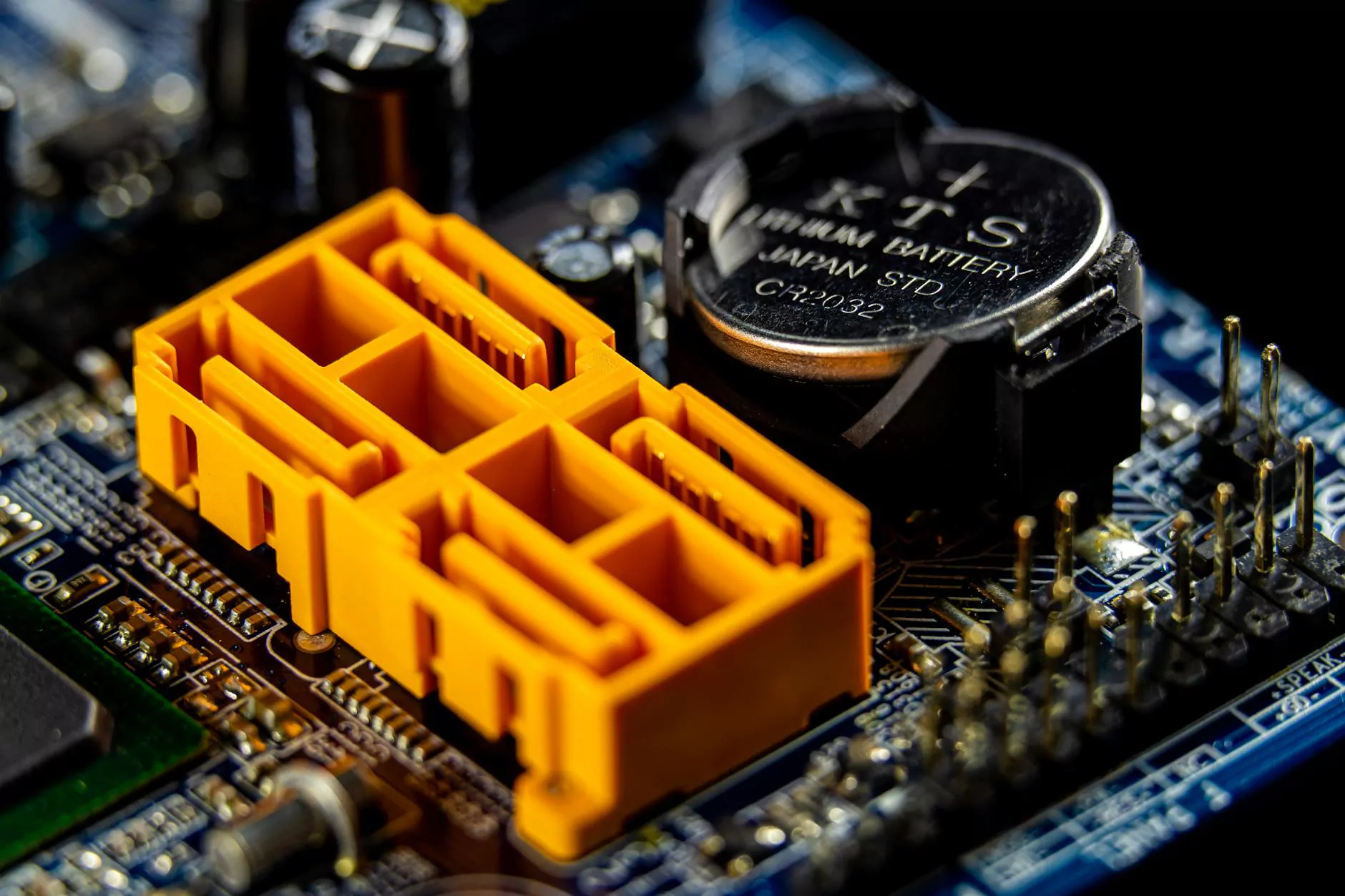
The realm of business increasingly emphasizes innovation, precision, and adaptability. One niche that has gained immense traction is that of silicone prototype manufacturers. These specialized companies are not just producers; they are crucial players in the landscape of product design, shaping the future through experimentation and technology.
Understanding Silicone Prototyping
Silicone prototyping involves creating functional prototypes using silicone materials. This process offers several advantages:
- Durability: Silicone is known for its strength and flexibility, making it ideal for testing purposes.
- High Fidelity: Prototypes can closely mimic the final product, allowing for better testing and validation.
- Speed: Silicone prototypes can often be produced quickly, crucial for time-sensitive projects.
The Importance of Prototype Manufacturing in Product Development
In the competitive landscape of product design, effective prototyping can mean the difference between success and failure. Here are key reasons why silicone prototype manufacturers are vital:
1. Accelerated Development Cycles
The modern market requires rapid turnaround times. Silicone prototypes allow designers to conduct tests and receive feedback much faster than traditional manufacturing methods. This not only accelerates the development cycle but also enhances overall product quality.
2. Cost-Effectiveness
Investing in initial prototypes is often a fraction of the cost compared to full-scale production. By utilizing silicone prototype manufacturers, businesses can identify flaws early in the design process, potentially saving thousands of dollars.
3. Enhanced Collaboration
Prototyping fosters collaboration across departments. Engineering, marketing, and design teams can work together using silicone prototypes to align their vision, ensuring that everyone is on the same page before moving forward.
Applications of Silicone Prototypes
Silicone prototypes find applications across various industries:
Medical Devices
In the medical field, where precision is paramount, silicone prototypes are used to create realistic models for testing medical devices, ensuring functionality and safety before larger investments are made.
Consumer Electronics
As technology evolves, consumer electronics require rapid iterations. Silicone prototypes enable manufacturers to explore ergonomic designs and functionality, ensuring that products meet the market's ever-changing demands.
Automotive Industry
The automotive industry relies on robust prototyping for everything from interior components to exterior features. Silicone prototypes help streamline testing processes, contributing to the development of safer, more innovative vehicles.
Choosing the Right Silicone Prototype Manufacturer
When selecting a manufacturer, consider these crucial factors:
1. Experience and Expertise
Look for manufacturers with extensive experience in your industry. Their background can provide insights into best practices and innovative solutions. The right silicone prototype manufacturers will bring both artistic vision and technical prowess to the table.
2. Quality Assurance Practices
Effective quality control measures ensure that prototypes meet specifications and performance standards. Inquire about the quality assurance processes your potential manufacturers employ.
3. Flexibility and Responsiveness
Your manufacturing needs may evolve, and the best prototypes come from manufacturers who are flexible and responsive. They should be willing to adapt to your changing requirements seamlessly.
Incorporating 3D Printing with Silicone Prototyping
The integration of 3D printing technology with silicone prototyping has yielded impressive results, pushing innovation further:
1. Rapid Prototyping
3D printing allows for quick iterations and easy modifications, facilitating the development of silicone prototypes. Designers can print complex geometries and test them in real time.
2. Customization Options
Silicone prototype manufacturers can easily customize designs using 3D printing techniques, accommodating specific requirements, whether they pertain to size, texture, or functionality.
Future Trends in Silicone Prototyping
The future of silicone prototyping holds immense potential as emerging technologies evolve. Some trends to watch include:
- Integration with AI: Artificial intelligence can optimize design processes, making prototyping more efficient and intuitive.
- Eco-friendly Materials: There is a growing demand for sustainable materials in production processes. Silicone prototyping is expected to evolve with alternative, eco-friendly options.
- Advanced Simulation Techniques: Improved simulation technology will enable manufacturers to test prototypes virtually, saving time and resources.
Conclusion
As the world becomes increasingly driven by technology and rapid product turnover, the role of silicone prototype manufacturers will only continue to grow. Their ability to produce high-quality, functional prototypes significantly impacts product design, adding immense value to businesses across various sectors.
At arti90.com, we are committed to embracing these innovations and providing our clients with unparalleled design and manufacturing solutions. By leveraging our expertise in art supplies, product design, and 3D printing, we aim to empower businesses to navigate the evolving landscape with confidence and creativity.
With the strategic utilization of silicone prototypes in product development, businesses can remain competitive and responsive to market demands. The future is bright for those who are willing to innovate and adapt!