Electric Plastic Molding: Revolutionizing Manufacturing
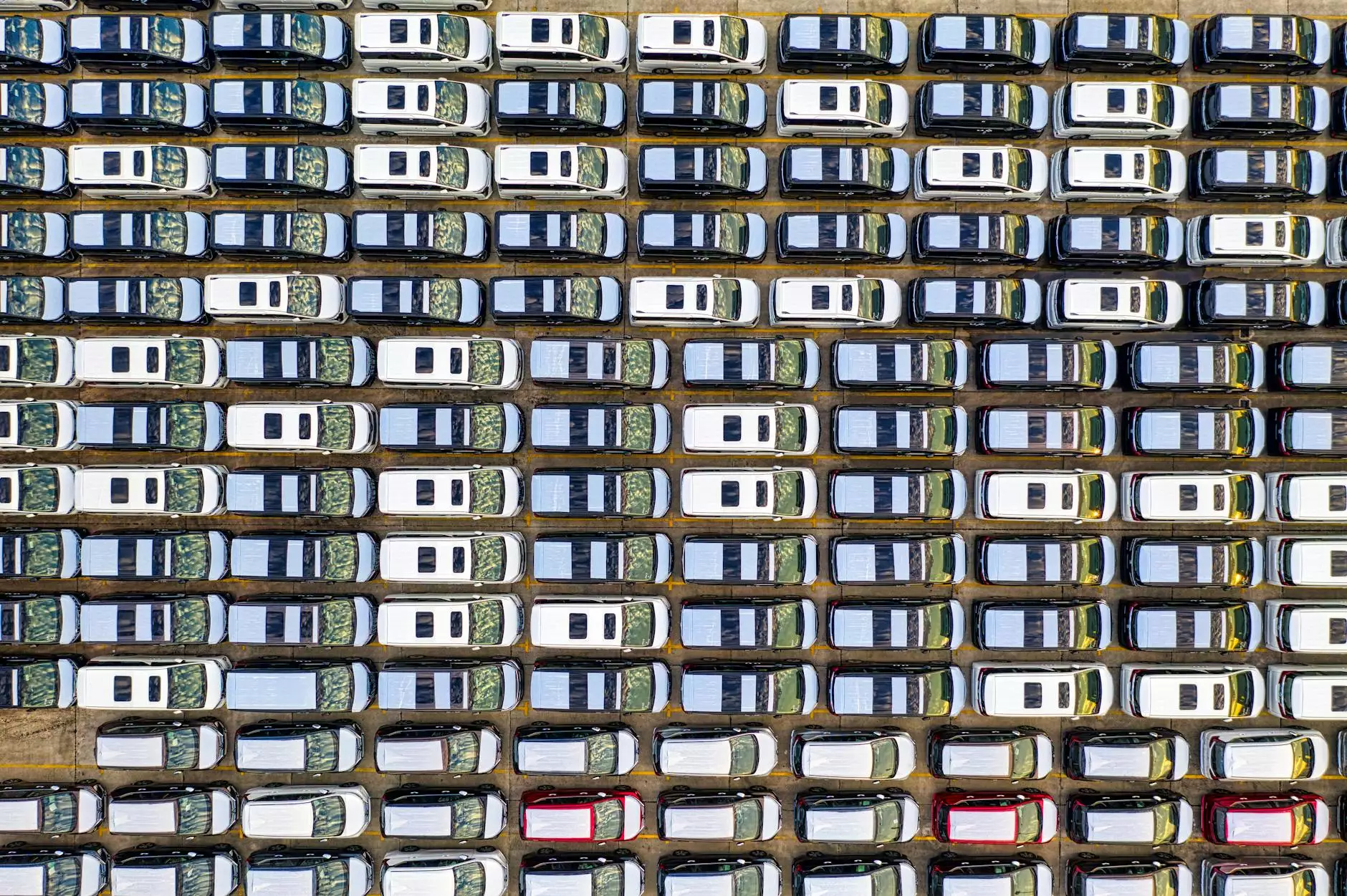
In today's rapidly evolving industrial landscape, Electric Plastic Molding is emerging as a transformative solution in manufacturing. This process not only enhances efficiency but also reduces environmental impact, making it a favored choice among manufacturers globally.
Understanding Electric Plastic Molding
Electric Plastic Molding refers to the use of electric energy to power the molding machines that shape and form plastic materials into desired objects. Unlike traditional hydraulic molding, electric molding machines offer precision, efficiency, and sustainability. The way this process works is intricate yet fascinating:
- Power Source: Instead of hydraulic systems, electric machines utilize servo motors that precisely control the molding process.
- Energy Efficiency: These machines consume less energy, leading to lower operational costs.
- Precision: Electric molding provides enhanced control over the process, resulting in less waste and higher-quality products.
The Advantages of Electric Plastic Molding
The adoption of Electric Plastic Molding brings several advantages that can significantly improve product quality and operational efficiency:
1. Enhanced Energy Efficiency
Electric molding machines are designed to consume up to 50% less energy than their hydraulic counterparts. This reduction in energy consumption is not only beneficial for the manufacturer’s bottom line but also contributes to less environmental pollution.
2. Improved Precision and Quality
With the ability to achieve extremely accurate movements and control, electric molding ensures that products are made to precise specifications. This leads to lower rejection rates and higher overall quality, crucial for businesses focused on perfection.
3. Reduced Maintenance Costs
Electric machines generally require less maintenance compared to hydraulic systems. Fewer moving parts result in lower wear and tear, which means reduced downtime and maintenance budgets for manufacturing facilities.
4. Environmentally Friendly
Using electrical energy helps reduce the carbon footprint associated with traditional manufacturing processes. The lesser requirement for hydraulic oil usage further diminishes the environmental impact.
Applications of Electric Plastic Molding
The versatility of Electric Plastic Molding allows for a wide range of applications across various industries. Some notable applications include:
- Automotive Components: Molding of parts like dashboards, panels, and containers.
- Consumer Electronics: Production of sophisticated components for devices like smartphones and laptops.
- Medical Devices: Precision components for medical equipment, where quality and accuracy are paramount.
- Packaging: Creating complex packaging solutions that require high precision and speed.
Why Choose deepmould.net for Electric Plastic Molding?
At deepmould.net, we are committed to advancing the standards of Electric Plastic Molding and serving our clients in the best possible manner. Here are reasons to consider partnering with us:
1. State-of-the-Art Technology
We invest in the latest electric molding technologies to ensure our processes are efficient and produce top-quality products. Our commitment to innovation keeps us at the forefront of the industry.
2. Expert Team
Our team is comprised of industry experts who understand the nuances of Electric Plastic Molding. Their expertise ensures that every project meets the highest standards of excellence.
3. Customized Solutions
We recognize that every client has unique needs. Hence, we offer tailored solutions that align perfectly with your specific requirements, ensuring maximum satisfaction.
4. Competitive Pricing
While we prioritize quality, we also believe in offering competitive pricing. Our efficient processes allow us to pass cost savings onto you without compromising on quality.
Future Trends in Electric Plastic Molding
The future of Electric Plastic Molding is bright, with several trends anticipated to shape its evolution:
1. Smart Manufacturing
The integration of IoT and AI into manufacturing processes is set to revolutionize Electric Plastic Molding. Smart machines will analyze production data in real-time, optimizing processes and increasing efficiency.
2. Sustainable Practices
As the world moves towards sustainability, electric molding processes are expected to further adopt eco-friendly practices, from material selection to waste reduction strategies.
3. Enhanced Material Capabilities
With ongoing research, new materials compatible with Electric Plastic Molding are emerging, expanding the potential uses and applications even further. This opens doors for industries to create innovative products.
Conclusion: Embracing the Benefits of Electric Plastic Molding
Electric Plastic Molding offers unparalleled advantages that can elevate manufacturing standards within various industries. Its benefits, ranging from energy efficiency to superior quality control, make it an ideal choice for modern production needs. By partnering with industry leaders like deepmould.net, businesses can leverage this cutting-edge technology to thrive in an increasingly competitive market.
In summary, the shift towards electric molding technology represents not just a trend but a fundamental change in how products are manufactured. Embrace this change today and watch your business flourish.